오늘은 PE 튜브에 관해서 같이 알아보고자 합니다.
화장품 PE 튜브 용기는 화장품 제품을 담는 용기로, 폴리에틸렌(PE)으로 만들어집니다. PE는 가볍고 유연하며 내구성이 뛰어나고, 화학적 안정성이 높아 내용물과의 반응을 최소화합니다. 이 용기는 다양한 크기와 디자인으로 제작될 수 있어 화장품 브랜드들이 다양한 제품에 활용할 수 있습니다. 또한, 튜브 형태로 인해 사용이 편리하며, 내용물 토출량을 사용자가 직접 조절할 수 있으며 끝까지 토출할 수 있다는 장점 때문에 많이 사용되는 용기 중 하나입니다.
특히 PE 튜브 용기는 다른 화장품 용기류에 비해서 가장 저렴하게 만들 수 있으며 금형 투자를 하지 않아도 되며 인쇄면이 넓어서 브랜딩 디자인 적용이 용이하다는 장점 또한 제조사에서 많이 사용되는 이유입니다.
이렇듯 튜브 용기는 다양한 장점을 갖고 있습니다. 본 칼럼에서는 튜브 용기 중의 하나인 PE 튜브 용기에 대해 생산 방식부터 특징, 단가, 생산업체, 장단점등을 정리해 보겠습니다.
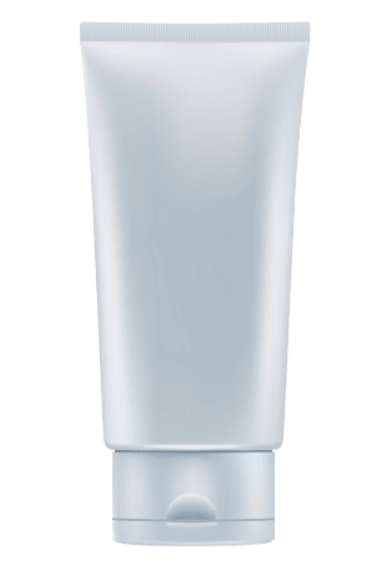
튜브 용기에는 크게 압출 방식의 PE튜브, 필름 접착 방식의 라미튜브(업계용어)로 나뉩니다. 생산 방식이 완전히 달라서 설비도 다르며, 공장도 분리되어 있습니다. 물론 두가지를 모두 생산하는 공장도 많이 있습니다. 여하튼 두가지의 생산방식이 완전 다르기 때문에 디자인을 하는 방식, 인쇄 방식, 후가공 방식, 재질, MOQ까지 차이가 크게 있습니다.
–
PE 튜브 용기 의 장점
- 유연성
PE는 반결정성 고분자로, 일정 부분 결정성과 비결정성 영역을 함께 가지고 있어 탄력성과 유연성이 탁월합니다. 이러한 특성 덕분에 튜브를 쉽게 압축할 수 있으며, 사용자가 내용물을 원하는 만큼 짜낼 수 있습니다. 그래서 사용이 편리하고, 내용물을 효율적으로 사용할 수 있습니다. - 내구성 & 휴대성
PE는 강한 결합을 가진 고분자 구조로 되어 있어 충격이나 압력에 잘 견딥니다. 특히 휴대하거나 떨어뜨릴 때도 일반 유리용기나 PET 용기처럼 파손되지 않고, 제품을 안전하게 보호할 수 있습니다. 내구성 덕분에 장기간 사용이 가능하며, 제품의 품질도 오래 유지할 수 있습니다. - 화학적 안정성
PE는 비극성 물질로, 대부분의 화장품 성분과 반응하지 않습니다. 이는 내용물이 PE와 접촉해도 화학적 변화가 일어나지 않음을 의미하며, 화장품의 품질과 안정성을 보장합니다. PE는 산성이나 알칼리성 성분과도 안정적으로 유지됩니다. - 경량
PE의 밀도는 약 0.91-0.96 g/cm³로, 다른 많은 플라스틱보다 가볍습니다. 이 경량성은 휴대성을 높여주며, 특히 여행용 화장품이나 휴대가 중요한 제품에 유리합니다. 또한, 가벼운 소재는 운송비 절감에도 기여합니다. - 다양한 압출 컬러
PE는 가공이 용이한 소재로, 다양한 방법으로 성형할 수 있습니다. 열가소성 특성 덕분에 고온에서 쉽게 변형되고, 냉각 시 원하는 형태로 고정됩니다. 그래서 원료에 색상을 넣어 연출하기에 비교적 간편한 편입니다. 다만, 투명도가 없기 때문에 Solid 컬러만 연출하겠다면 다양한 컬러를 테스트해보며 원하는 색상을 뽑아낼 수 있습니다. - 재활용 가능
PE는 열가소성 수지이기 때문에 재활용 공정에 적합한 플라스틱 재료입니다. 다만, 재활용센터에서 캡과의 분리, 내용물의 혼입, 나사선 부분의 PP재질 때문에 최근에는 재활용 불가능 품목으로 분리되고 있습니다. - 비용 효율성
PE는 원료가 비교적 저렴하며, 생산 공정이 단순하고 효율적입니다. 대량 생산 시에도 비용이 크게 증가하지 않으므로 경제적입니다. 따라서 개발 비용과 생산원가가 저렴해서 다른 화장품 포장재에 비해 가장 경제적으로 사용할 수 있습니다.
–
PE 튜브 용기 의 단점
- 기체 투과성
PE는 특정 기체(산소, 이산화탄소 등)에 대해 완전히 차단하지 못합니다. 이는 일부 화장품 제품이 산소와 반응하여 산화되거나, 향이 빠져나가는 등의 문제가 발생할 수 있음을 의미합니다. 그래서 최근에는 기체 차단제인 EVOH를 중간에 삽입한 5겹 PE튜브를 사용합니다. - 온도 민감성
다음 내용은 브래닛 사이트에서 확인하세요~
–
답글 남기기